論文/高精度完全試験
精度の高い無菌濾過フィルターの完全性試験手法について
- 1.はじめに
- 2.完全性試験の種類
- 3.親水性無菌濾過フィルターに用いられる完全性試験の原理、手法と問題点
- ディフュージョンフロー試験
- バブルポイント試験
- 4.疎水性無菌濾過フィルターに用いられる完全性試験
- ディフュージョンフロー試験
- バブルポイント試験
- ウォーターイントルージョン試験
- ウォーターフローディフュージョン試験
- 5.完全性試験の有効性
- ディフュージョンフロー試験
- バブルポイント試験
- ウォーターイントルージョン試験
- ウォーターフローディフュージョン試験
- 6.精度の高い無菌濾過フィルターの完全性試験手法
『マスフローコントローラー(MFC)式完全性試験』
- ディフュージョンフロー試験への適用
- バブルポイント試験への適用
- ウォーターイントルージョン試験への適用
- ウォーターフローディフュージョン試験への適用
- 7.無菌濾過フィルターに求められる品質保証値
- 8.PAT(工程解析技術)における完全性試験のあり方
- 9.さいごに
1.はじめに
無菌濾過フィルターの完全性試験は、薬液濾過の前後に行うことで薬液中の微生物を除去出来るか、更にはできたか否かを予測するため、非破壊的に実施される。無菌濾過フィルターの完全性試験が有効な手段であることは、長年にわたり製薬業界で認識されている。
完全性試験は毛細管現象を利用した手法であるが、フィルターユーザーはその原理と、何故微生物除去性能の予測が可能なのかを正しく理解する必要がある。そして得られた完全性試験データを解析し、正しく運用する事が肝要である。完全性試験が真に無菌濾過フィルターの完全性を検証することができれば、PAT(工程解析技術)における有効な手段になりうると考えられる。例えば、濾過行程に於いて完全性試験で不具合が起きた場合、試験不良の原因を検知し、解析できるようなシステムを構築する事が重要である。
本稿では完全性試験の種類、原理、有効性(相関関係)、手法について親水性無菌濾過フィルター及び疎水性無菌濾過フィルターを対象に述べる。更に理論的、合理的な「完全性試験」を求めた「マスフローコントローラー(MFC)」を用いた精度の高い無菌濾過フィルターの完全性試験手法について報告する。
2.完全性試験の種類
無菌濾過フィルターには2つの相反する特性を有するものがある。
一つは主に液体濾過に用いる親水性のメンブレンフィルターであり、他方は主として空気等、気体濾過に用いる疎水性メンブレンフィルターである。
A.親水性メンブレンフィルターに用いられる完全性試験
- ディフュージョンフロー(DF)試験(フォワードフロー試験とも呼ばれる)
- バブルポイント(BP)試験
B.疎水性メンブレンフィルターに用いられる完全性試験
- ディフュージョンフロー(DF)試験「IPA(イソプロピルアルコール)使用」
- バブルポイント(BP)試験(IPA使用)
- ウォーターイントルージョン試験
- ウォーターフローディフュージョン試験
上記の完全性試験はいずれも濾過膜の毛細管現象を利用した試験手法である。
3.親水性無菌濾過フィルターに用いられる完全性試験の原理、手法と問題点
A.ディフュージョンフロー(DF)試験
原理
DFとは、水等で十分に湿潤した無菌濾過フィルターの膜面に空気又は窒素ガスで加圧(BP管理基準値の80%程度の指定圧力)すると、膜内に孔径により異なる高さの水柱が形成される。この水柱の一次側は高圧に、二次側は大気圧となっているため、高圧側の気体が水膜中に拡散し、高圧側から大気圧側へ向かって水膜中を加圧気体が透過していく現象を言う。無菌濾過フィルターの孔が大きければ水柱は低くなり、DF量は多くなる。また、小さければ水柱は高くなり、DF量は少なくなる。
手法
十分に湿潤した無菌濾過フィルターにメーカー指定の気体圧力(通常圧縮空気又は窒素ガスが用いられる)をかけ続け一定に保つ。するとフィルターの二次側から加圧気体が無菌濾過フィルター内の水膜中を拡散現象により透過流出してくる。この時の単位時間当りの気体流出量を測定し、その量がフィルターメーカーで実施するバクテリアチャレンジ試験結果から、メーカーが規定する管理基準値以内かどうかで合否判定を行う定量的手法である。製造プロセスの中での本試験法の運用に当っては、加圧圧力によってDF量が増減するため、気体の圧力を如何に一定に保持することが出来るかは非常に重要である(グラフ1)。
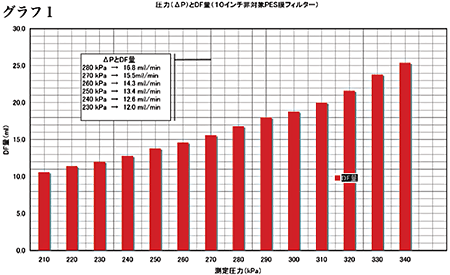
適用上の問題点
無菌濾過フィルターのメーカーは完全性試験管理基準値を決めるための相関試験データを10インチカートリッジを用いて実施している。その管理基準値は一定の規定圧力下に於いて、 DF値≦○○m2/min で表される。
つまりDF管理値は最大値が用いられ、フィルターメーカーは管理基準値以下の性能を有するフィルターをユーザーに供給する事になる。このことは20インチ以上のマルチカートリッジが使用される場合に以下のような問題が考えられる。
例えば、20インチカートリッジを例にとると、図1に示すようなケースがあったとしたら、マルチフィルターを構成する個別のフィルターに不合格品があっても、20インチカートリッジとして合格となってしまう。このような事を考慮し、20インチは10インチの2倍のディフュージョン量としていないメーカーもあるが、それだけで万全とはいえない。また、製造時において、フィルターメーカーは各10インチカートリッジの段階で圧力(ΔP)とDF量(10インチ非対象PES膜フィルター)
1回、マルチカートリッジに組み上げてもう1回の完全性試験を出荷前検査として実施しているが、出荷後の不測の事故を防止するためにユーザーサイドでフィルター使用前後に完全性試験を行う事が求められている。ちなみに10インチカートリッジ単体の試験でさえ不合格となる事例があるという事実は、DF試験のマルチカートリッジに対する有効性に「理論的限界」がある事を示している。すなわち、DF試験は10インチカートリッジフィルターまでに適用を限定する手法と言える。それ故、マルチ濾過システムを構築せざるを得ない場合は、ピンホールが検出可能な試験を組み合わせる等の対策を講じる必要があると考える。
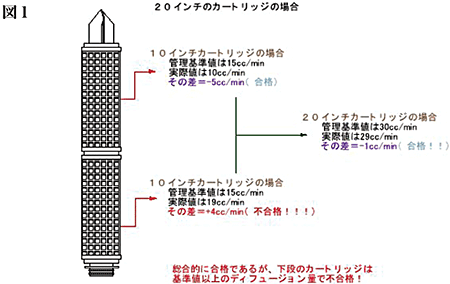
B.バブルポイント(BP)試験
原理
BPとは、十分に湿潤した無菌濾過フィルターの一次側から空気又は窒素ガスで加圧していく。圧力の上昇に伴い無菌濾過フィルターの毛細管内の湿潤液が二次側に向かって押し出されていく。湿潤液は、最終的に毛細管の孔から二次側へ排出されることになるが、この圧力が湿潤液の表面張力に勝って二次側に排出される時の圧力をBPという。孔の大きさと湿潤液の表面張力の関数で
手法
十分に湿潤した無菌濾過フィルターに加圧気体で出来るだけゆっくりと昇圧していく。概ね10~20kPa/分の昇圧速度が望ましい。昇圧速度を速くするとデータ分解能が低下する。この時のガス供給量は一定に保たなければならない。昇圧初期の低圧状態ではDFはほとんど発生せず、グラフにプロットした場合直線状の圧力上昇線が得られる。昇圧を継続していくと徐々にDFが発生し、圧力上昇グラフは曲線を描く。この曲線はDFカーブと呼ばれるもので概ね二次曲線となる。曲線が一定の変化率でカーブを維持している間はDFの状態でBPではない。BPに達するとDFカーブ中に変曲点が生じる。最初の変曲点を生じる時の圧力がファーストBP(BP1)と呼ばれている。この時の気体リーク量は極僅かで、圧力上昇は継続していくが、圧力上昇に伴い順次小さな孔からもBPが発生していく(BP2・・・BPn)。この変曲点を圧力上昇グラフから判別する事は非常に困難であり、サブミクロンの微細孔の検知にはいかに美しいDFカーブを得るかという技術と、各圧力サンプリング点の変化率をより明確に判別する技法が必要となる。尚、フィルターメーカーの規定するBPの管理基準値はDF試験同様、バクテリアチャレンジ試験の結果から求められ、BP≧管理基準値で表される。
適用上の問題点
DF試験が定量的試験であるのに対し、BP試験は理論的には0.2μm以上の一つの孔を発見できる定性的試験法である。BP試験法は非常にデリケートな試験法であり、濾過面積の大きい(DF量の多い)カートリッジタイプのフィルターの場合、目視で検証する事は不可能に近い。濾過面積が大きくなるに従いDF量は大きくなり、目視によるBPの判断は更に困難となる。これを克服するため、目視で検証できるDF試験法が考案された歴史的背景がある。BP試験に真に求められる事は、無菌濾過フィルター内に存在するかもしれない0.2μmより大きい孔の検出である。無菌濾過フィルター内に菌が漏洩する大きさの孔(ピンホール)が存在すれば、流体力学的にもそのピンホールからの薬液透過量は最も多くなり、濾液側への菌の漏洩の危険性は大きくなる。いかにこのピンホールを検出するかは重要事項である。しかし今までの技術水準では最大孔を示すBP1ではなく、段階的、継続的にBPが発生するBP1~BPnとして検出する事しかできなかったため、BP1がBP群の中に埋没してしまうという問題がある。
4.疎水性膜無菌濾過フィルターに用いる完全性試験
A.ディフュージョンフロー試験(IPA使用)
フィルターメーカー指定の比率のIPAと水の混合液を用い無菌濾過フィルターを十分に湿潤させる。以降は親水性無菌濾過フィルターと同様の手法並びに適用上の問題点を有する手法である。
B.バブルポイント試験(IPA使用)
フィルターメーカー指定の比率のIPAと水の混合液を用い無菌濾過フィルターを十分に湿潤させる。以降は親水性膜と同様の手法並びに問題点を有する手法である。
C.ウォータ-イントルージョン試験
原理、手法
疎水性無菌濾過フィルターの一次側を水で満たし、計測ライン一次側から高圧気体を用いフィルターメーカーの指定圧力まで昇圧する。水の流出が二次側から確認できるようになるまでの安定時間を経た後、二次側からの水の流出量を計測し合否判定を行う。二次側に流出した水の量で判定するため特別の器具は必要なく、測定者の個人間に於ける誤差も少ない。
適用上の問題点
二次側を開放する必要があり、インライン測定では完全性試験機を使用する必要がある。二次側への水の流出水が無菌濾過フィルターのプリーツに滞留することを考慮しなければならない。その間の安定時間を必要とする比較的長時間を要する手法である。
D.ウォーターフローディフュージョン試験
原理、手法
新しい疎水性無菌濾過フィルターはある圧力まで水を透過させないという特性を利用した試験法である。疎水性無菌濾過フィルターの一次側を水で満たし、その上部に高精度のエアーメスシリンダーをセットする。計測ライン一次側から高圧窒素ガスを用いフィルターメーカーの指定圧力まで昇圧し、その圧力を維持する。この時、疎水性膜の内部に水が浸透していく。その量は極微量である。高精度のエアーメスシリンダー内の水柱の移動量を計測し、基準値以内であるか否かで合否判定を行う。二次側を開放する必要がないという点で、ウォーターイントルージョン試験法に比して優れた手法である。
適用上の問題点
得られる水の移動量は毎分1ml程度と非常に小さな値である。この試験法をインラインで実践するには、完全性試験機を使用することになるが、一次側容積の正確な測定、温度変化のない環境や測定圧力を一定に保持することが求められる。また、圧力センサーの精度が非常に重要になり、単位時間当りの水移動量が小さいため1パスカル単位での精度が要求される。しかしながら、この単位で圧力センサーのキャリブレーションを行う事は国家標準器をもってしても不可能である。
5.完全性試験の有効性
医薬品製造工程に於ける完全性試験は、フィルターメーカーが提供する相関データと手法的に相関性があることが求められる。
A.ディフュージョンフロー試験
フィルターメーカーが提供するDF試験の相関データは一次側気体圧力を一定に保持する手法で得られている。それ故医薬品製造の実工程内試験で一次側気体圧力を一定に保持する事は重要で、これにより相関データと医薬品製造工程に於ける完全性試験の間に「相関性」が保たれる。無菌濾過フィルター膜面に一定の気体圧力を保持する事で常に一定のDF量を得る事が可能となる。完全性試験に求められる手法の一致という点に於いても必要な要件である。
B.バブルポイント試験
バブルポイント試験の定義は、曖昧に表現され手法も具体的に明らかにされていない。「連続的に気泡が発生する圧力点」と定義される場合が多いのであるが、これではピンホールの発見は困難である。そもそもバブルポイント試験法は、一つの微細な大きさの孔を検知するための定性的手法である。無菌濾過フィルターは非常に均一な微細孔で形成されているという前提から、均一な微細孔の群として検知する手法が用いられていると思うが、これが現在の技術的な限界である。真に重要な事は菌がリークする可能性のある大きさのピンホールの検出である。
C.ウォーターイントルージョン試験
本試験は二次側への水の流出量を見る手法であるため、一次側圧力に注意さえすればオフラインでは比較的容易に実施できる試験法である。インラインでは二次側を開放する事が出来ないため完全性試験機を使用する事になるが、採用される合否判定基準値は非常に小さな数値であるため、出力された数値が適正なものであるかどうかを検証する必要がある。
D.ウォーターフローディフュージョン試験
本試験の最大の特性は疎水性膜の濾過前試験が可能な事である。従前の疎水性無菌濾過フィルター完全性試験手法(BP法、DF法)はIPA溶液を用い、湿潤液の表面張力を下げないとフィルターを湿潤できず完全性試験を行う事が出来なかった。IPA溶液を使用し無菌濾過フィルターを湿潤することは、疎水性の回復やIPAの洗浄除去が困難なことによりフィルターの破壊試験に等しい。その点ウォーターフローディフュージョンテストは膜内を湿潤させていないので非破壊的試験である。一次側の水を排出すれば、再度その無菌濾過フィルターを使用することができる。ウォーターフローディフュージョン試験で採用される合否判定基準値は非常に小さな数値であるため、得られた数値が適正なものであるかを検証する必要がある。
6.精度の高い無菌濾過フィルターの完全性試験手法
『マスフローコントローラー( M F C ) 式完全性試験』
MFCとは窒素ガスや圧縮空気の流量を質量で計量し、且つ制御バルブを調整する事により任意の気体質量を供給する事が出来る装置である。気体を質量で計測できる事から、供給する気体の温度・圧力に関係なく25℃、単位時間当りの標準状態の気体流量として計量する事が出来る。このシステムを応用し、各種完全性試験に求められる機能を構築した試験手法について述べる。
A.ディフュージョンフロー試験への適用
比例積分フィードバック制御を採用する。
試験対象無菌濾過フィルターを十分に湿潤させた後、一次側から測定用加圧気体を供給する。一次側圧力が上昇するに伴いフィルターからのDFが発生していくが、圧力センサーとリンクしたMFCは指定の圧力に達するとガス供給量を減ずる。MFCからのガス供給量がDF量よりも少ないと測定ライン一次側圧力は低下する。この圧力低下を検知した圧力センサーは制御系に信号を送りガス供給量を増加させる。指定圧力よりも圧力が下がればガス供給量を増加、圧力が上がれば減少という作業を繰り返し行う。こうしたフィードバック制御を繰り返し、指定された圧力を一定に保持できる気体供給量を探査していく(図2)。この間、完全性試験機と対象フィルター間の距離による圧力の差位も平衡化されていく。そして、圧力も指定圧力近傍に保持され、ガス供給量も一定に保持することが2分間継続された事実を以て「収束条件」とする。この時点で気体供給量とフィルターからのDF量は等しくなっている(図3)。
本手法は非無菌区と無菌区の間の疎水性無菌濾過フィルター(ベントフィルター)の冷却時間を必要としないというメリットがある。圧力センサーからの圧力上下動の情報はCPUに集約され、CPUはその情報に基づきMFCからの気体供給量をフィードバック制御する。この一連の制御は非常にリニアに実施、測量されるため、SIP後のベントフィルター内の経過時間に伴う熱収縮による気体の体積変化はほとんど無視できる(図4)。従って、SIP後測定対象フィルターを湿潤した後は即時に完全性試験が実施できる。DF試験に於いて、MFC方式には多数のメリットがある。
- SIP後、ベントフィルターが冷却するまで待つ必要がない。
- 「相関性ある完全性試験」が実践できる。
- 試験配管系内の熱的影響を受けないで試験を実行できる(温度補正計算不要)。
- 試験配管系内に漏気部がある場合、モニタリングにより容易に特定可能。
- 大容量のMFCを採用する事で多数のカートリッジフィルターラインにも適用する事ができる。
B.バブルポイント試験への適用
試験対象フィルターを十分に湿潤させた後、一次側から測定用加圧気体を供給する。比例積分制御により一分間に約20kPaの圧力上昇が得られるように一定の気体供給量を調節する。このことはグラフに時間と圧力上昇の値をプロットした時に、常に一定の傾きの直線を得るために重要である(図5)。これにより再現性の高いデータを得る事ができる。DFが発生する前の圧力上昇グラフは直線状に上昇する。DFが始まると、圧力上昇線は次第に二次的な曲線を示す。これをDFカーブと称する。BP1はこの曲線中に生ずる最初の変曲点としてとらえられる。すなわち圧力上昇に伴い、規則的にDFが増加する間は曲線に規則性がある。しかる後、BPが発生すると曲線の規則性が損なわれるのである。変曲点は圧力上昇線からだけでは判別する事は困難で、二次的な処理を行う必要がある。具体的には圧力上昇値の変化率を二回微分をかけてグラフを作成しピンホールを検出する。無論、ピンホールが無く、いくつかの均一なBP群の孔が存在するフィルターでは最大孔径群をBP1群として検知する。分解能を高める処理法に付いては紙面の関係上割愛するが、ブラックボックス化する考えはないのでお問い合わせいただければ開示させていただく。図6は医薬品製造工程に於いてMFC式BP試験で0.4μm程度のピンホールを検出した記録の一例である。
高分解能及び再現性の高いグラフを表示、記録する事で完全性試験時に於ける「膜破損事故等」は容易に判別できる。実医薬品製造部門では、濾過後完全性試験で不合格となり「ロットアウト」となるケースがまま発生する。この原因としては完全性試験時、特にBP試験時におけるフィルターの破損に起因するものがほとんどと考えられる。BP試験は400~600kPaという濾過膜に対しては高圧の負荷試験である。膜破損の程度によっては、その状況はBP発生時と酷似している。このため完全性試験機が破損をBPとして判断し、その時の圧力値によっては「合格」を出力する。合格値を得たフィルターユーザーは安心して濾過を行うが、濾過後の試験で不合格という結果を突きつけられる事になる。一般に製薬に於ける濾過は定圧濾過である事が多い。しかも200kPa以下の事例がほとんどでフィルターにかかる負担は決して高くはない。最近では薬液適合試験も実施されている事も多く、このような事例で濾過後の完全性試験が不合格になる事はあってはならない事と言える。このようなロットアウトに直結するような事故が起こらないよう、最低限濾過前完全性試験で「膜破損」を認識できるようにする事は、いろいろな面で不可欠な事と言える。
BP試験に於いて、MFC方式には多数メリットがある。
- BP1を検知する事で無菌保証の精度が向上する。
- 微細なピンホールを検知する事ができる。
- 完全性試験時の膜破損を容易に検知する事ができる。
- BP試験を理論的に実践する事ができる。
- リアルタイムにトレンドグラフを表示、記録する事で試験の検証が容易にできる。
C.ウォーターイントルージョン試験への適用
本試験もDF試験同様MFCを使用することでより簡便化できる。フィルター二次側への水流出量は極僅かであり、試験配管系の温度変化がある程度あったとしても、リニアにMFCを調節することでこの影響を排除することができる。加圧圧力も自動的に設定値にコントロールすることができ、煩雑な圧力設定作業からも開放される。測定精度も非常に高く、グラフにより数値の理論的根拠を示すことも可能である。測定も比較的短時間ですみ、作業効率のアップに寄与している。
D.ウォーターフローディフュージョン試験への適用
基本的にウォーターイントルージョン試験と同様の手法で行い、同様のメリットがある。
7.無菌濾過フィルターに求められる品質保証値
無菌濾過フィルターは高度に理論化され、完全性試験管理基準値とバクテリア除去性能間に「相関関係」が確立されている。このバクテリア除去率の予測が可能なフィルターであるという理由から、広く医薬品濾過に使用されている。この「相関関係」なくして完全性試験は成立しえない。したがって、DFとBPを併用しなければならないと判断されたシステムに於いては、無菌濾過フィルターサイドにDFとBP各々にバクテリア除去性能を証明するデータが求められる。なぜならばDFとBPは理論的に異種なものであるからである。このことは理論式を見ても明らかである。また、BP試験はフィルター数が多くなると検証が困難な手法であるから、フィルターユーザーは完全性試験機のBP測定手法を吟味し、正当性を検証しておかなければならない。
8.PAT ( 工程解析技術) における完全性試験のあり方
現在は、相関データがある完全性試験手法を一種採用すれば適用上良しとされている。しかし各完全性試験は適用上の問題を孕んでおり、これらの問題点を解決することが「ロットアウト」等の重大事故を未然に防ぎ、多大な利益を失うことを防止することにもつながることになる。
10インチまでのフィルターシステムの場合はDF試験で「完全性試験」を実施するか、ピンホール検知そして膜破損を検出できるBP試験を行うことが望ましい。マルチ濾過システムではMFCを用いた「高精度な完全性試験」手法を用いたDF試験とBP試験を組み合わせることで理論的な不備を補填し合うことができる。「相関性」ある手法を用いることで高度に理論武装し、且つそれを高度に実践することが必要である。完全性試験機のIQ、OQとりわけOQについてはオフライン下で実施するのではなく、実際のプロセスラインを使用して行い、完全性試験機の動作確認とその適合性を見極めることが必要と考える。これにより試験配管系のリーク等が発見されることも多く見受けられ、配管改善のいいチャンスにもなるかと思う。そしてこれらのことを実践することで、PATにおける無菌濾過フィルターの完全性試験の構築が可能と考える。
9.さいごに
医薬品に於いてはより高度な品質管理並びに工程管理が求められる。無菌製剤に於ける無菌試験は、抜取り検査であり全数検査ではない。しかし、すべからく薬液は全量がフィルターを通過する。この点でフィルターの完全性の確認は必須事項であり、それは高い相関性をもって検証されなければならない。MFC方式が発明されたことにより、それが可能となった。図7に示すように医薬品製造に於ける「理論武装」という観点からも大きな進歩であると考える。
なお、MFC方式の手法はフィルテック株式会社が有する特許であり、本方式を採用した完全性試験機として「WINTESS-D®」がエーザイマシナリー株式会社及びフィルテック株式会社から販売されている。
以上
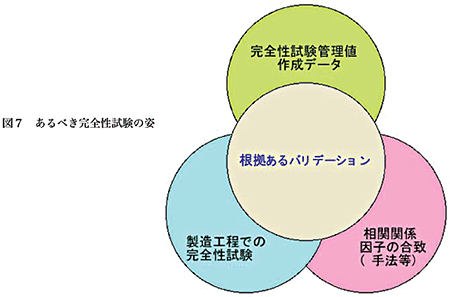